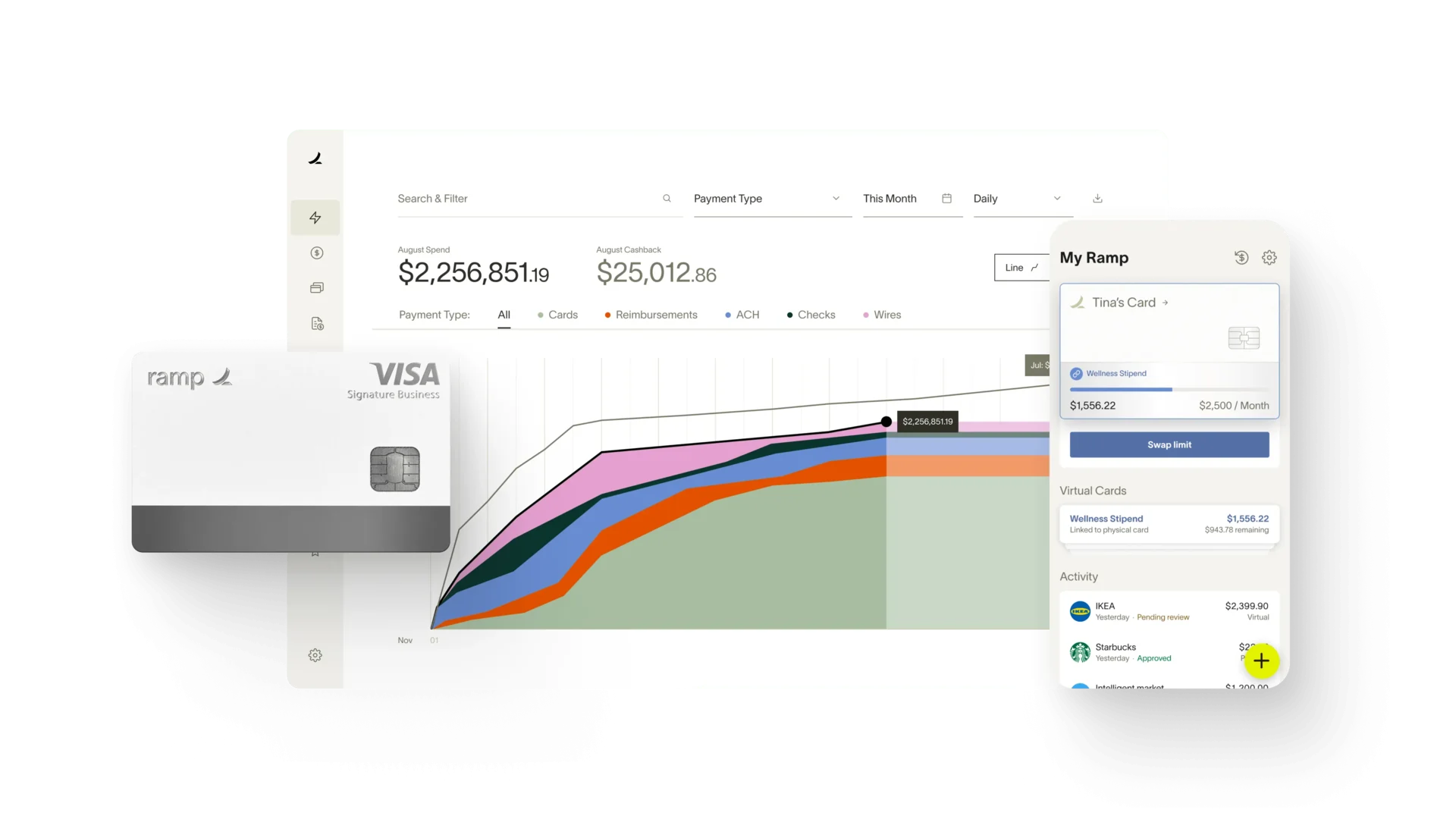
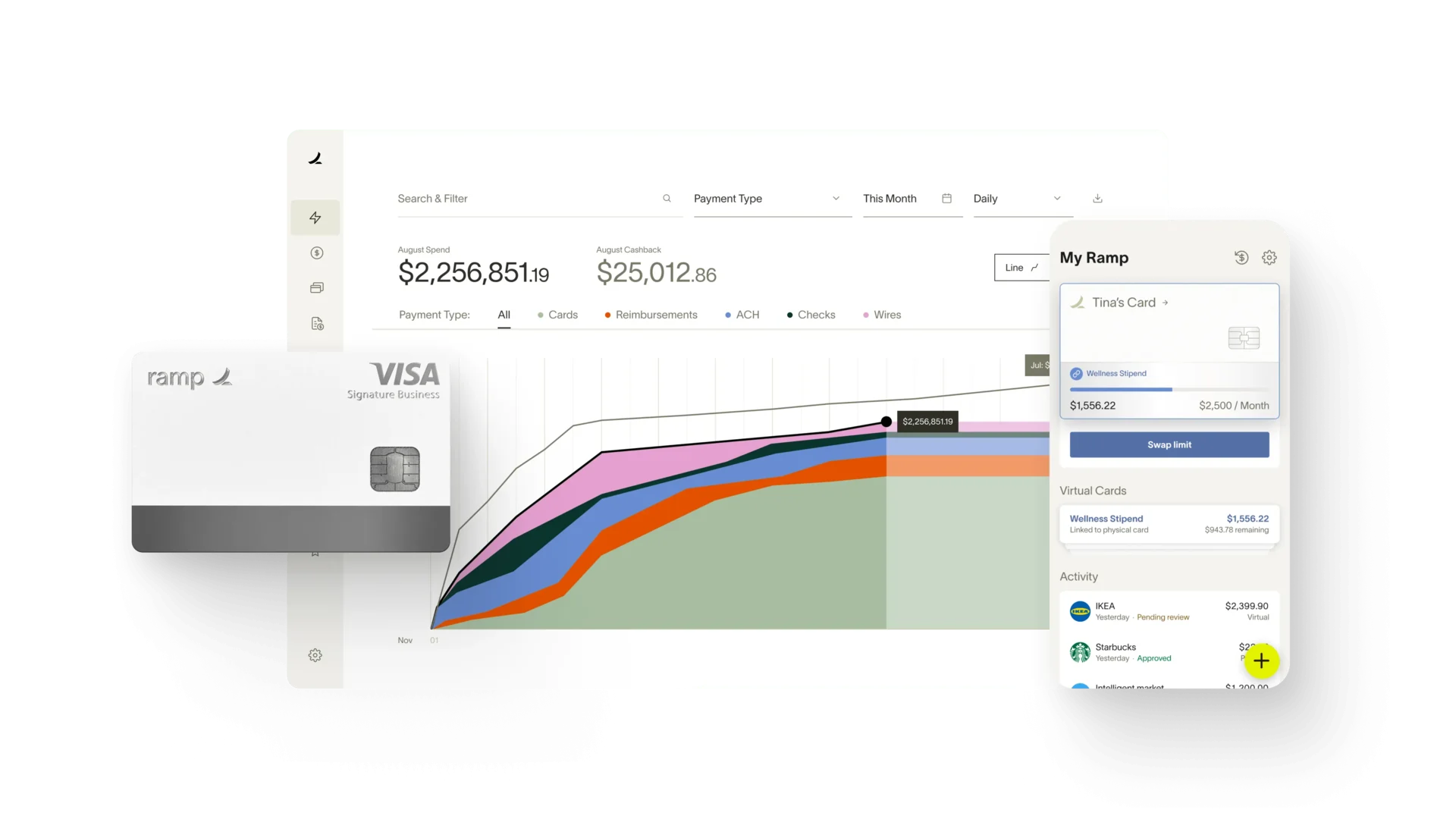
straight to your inbox
In the intricate dance of financial management within the manufacturing industry, expense reporting stands as a crucial choreography, where even the smallest missteps could lead to major financial dissonance. But what if you could automate this routine to not only reduce errors but also free up time for more value-added work? This guide is tailored for manufacturing professionals, finance managers, and operations teams who are ready to embrace the efficiency and accuracy that automated expense reporting can bring to their financial operations.
Storms of expenses can flood a manufacturing ledger from various departments — maintenance, procurement, and quality control, to name a few — creating a maze of receipts, numbers, and approvals. Navigating this labyrinth manually is not only time-consuming but also leaves your finance team vulnerable to human errors that often occur when tired eyes go through endless columns of digits. Automating your expense reporting can transform this maze into a transparent, well-lit path, fostering control, cost-advantages, and compliance. Let's embark on this journey together to streamline your manufacturing expense reporting process.
Step 1: Assess Current Expense Reporting Process
Before setting off, it’s crucial to map your starting point. Sit down with your team to review your current expense reporting process, aiming to pinpoint any bottlenecks and inefficiencies. To do so:
- Gather Data: Look back at historical trends of expense reporting. Are there certain spikes or drops in activity that can be attributed to seasonal changes, internal shifts, or external market forces?
- Listen to Feedback: Engage with employees who submit expenses and those who handle the reports. Their experiences can offer valuable insights into areas that need improvement.
- Run a Mock Audit: Simulate a compliance audit on your existing data. Are there any trends that the current system isn’t catching, potentially leading to regulatory mistakes or oversights?
The goal here is not just to identify what’s going wrong, but to understand why it’s happening. This understanding will be the compass that helps you navigate the change to automation.
Step 2: Research and Select an Expense Reporting Software
Choosing the right expense reporting software is a critical decision that will influence how smoothly the rest of the automation process unfolds. When selecting a tool:
- Consider Functionality: Look for platforms that offer robust expense tracking, reporting, and analytics features, capable of meeting the unique demands of a manufacturing environment.
- Check Integration Capabilities: The software must seamlessly integrate with your existing ERP, accounting, and payroll systems. Siloed data leads to fragmented insights and counteracts the very efficiency automation is meant to bring.
- Prioritize Usability: An intuitive user interface is key—complicated systems can lead to resistance from employees, which is the last thing you need when transitioning to a new process.
Remember, the best software is one that not only meets your needs now but can scale with your business as those needs grow and change.
Step 3: Customize Expense Categories and Approval Workflows
One size doesn’t fit all in manufacturing, and neither should your expense categories. Customize your system to be as granular as your business requires:
- Align Categories with Operations: Direct materials, maintenance parts, and supply chain expenses might need their own categories to enable better visibility and control.
- Set Granular Thresholds: Different departments may need different levels of scrutiny. Tailoring your approval workflows can ensure the right expenses are flagged for further review.
- Balance Control with Flexibility: Aim for a system that allows for deviations. Sometimes, the most critical expenses don’t fit neatly into a standard category, and the approval workflow should accommodate these exceptions seamlessly.
By customizing these details, you’re not just adapting your software to your business; you’re tailoring it to support the specific financial initiatives and strategies that make your manufacturing processes unique.
Step 4: Integrate Expense Reporting Software with Existing Systems
Integration is where the magic happens with an automated expense reporting system. A few things to keep in mind:
- Data Flow: Understand how data will move from the expense reporting software to your other systems. Real-time or batch updates can make a significant difference in ongoing operations.
- Testing: Rigorous testing ensures that the integration doesn’t break under the stress of live expense reports.
- Adaptation: Be prepared to tweak your expense reporting software and other integrated systems as you uncover areas that aren’t playing nicely together. Flexibility is key during this learning phase.
The effectiveness of the integration will ultimately dictate how well your new system delivers on cost and time savings, so invest in this step.
Step 5: Train Employees on Using the Expense Reporting Software
Training is the bridge that connects the promise of automation with the people who will make it a reality. To ensure a smooth transition:
- Offer Varied Learning Resources: From hands-on workshops to video tutorials, diverse training resources can cater to different learning styles and schedules.
- Run Pilots and Gather Feedback: Before a full rollout, small group pilots can highlight areas that need more attention and allow for in-the-field changes to be made.
- Foster a Learning Culture: Continuous improvement doesn’t end with the first training session. Encourage your employees to engage with the system, trial new features, and provide ongoing feedback.
Remember, the goal is not just to teach employees how to use the software but to instill confidence in the new process so that they become its advocates.
Step 6: Monitor and Analyze Expense Data
With your automated system humming along, it’s time to harvest the benefits of streamlined data:
- Real-Time Visibility: No more waiting for month-end reports. Use your new system to track expenses and make informed decisions as trends arise.
- Spot Anomalies: Automation doesn’t just make existing processes faster; it catches mistakes that might previously have gone unnoticed.
- Drive Strategy: Armed with detailed, accurate data, your finance team can now help drive cost-saving initiatives and operational efficiencies more effectively than ever before.
The analysis of expense data should not simply be retrospective but proactive, guiding your business towards smarter financial choices and agile cost management.
Conclusion
Embracing automation in your expense reporting can free your team from the drudgery of manual data entry and allow them to pivot towards more strategically valuable work. Manufacturing, with its intricate supply chains and operational complexities, stands to gain tremendous benefits from a well-designed, automated finance process. The journey to automated expense reporting may seem daunting, but with careful planning, strategic implementation, and ongoing optimization, the results will be transformative for your business.
So here's the call to action: Start the conversation within your teams, set your goals, and take the next step towards automating your manufacturing expense reporting. The investment of time and resources now will pay dividends as you unlock new efficiencies and direct more of your focus towards growing your manufacturing enterprise.